an integrated sawmill and pellet mill project
An Integrated Sawmill and Pellet MillForssjo Bruk AB manages an integrated sawmill and pellet-production plant on the Ericsberg Estates near Katrineholm in central Sweden. The sawmill annually consumes approximately 165,000 m3 of timber with 85% of the finished product exported. The pellet production system placed in service in 1995 has a capacity of about 45,000 metric tons per year. Pellets are sold in bulk for use in district heating plants and bagged for small-scale residential heating systems.
A 15-MW heating system fueled mainly with bark and wet wood chips provides heat for the drying kiln and for drying the sawdust prior to pelleting. Sawdust from the on-site milling operation, as well as other sources, are used.
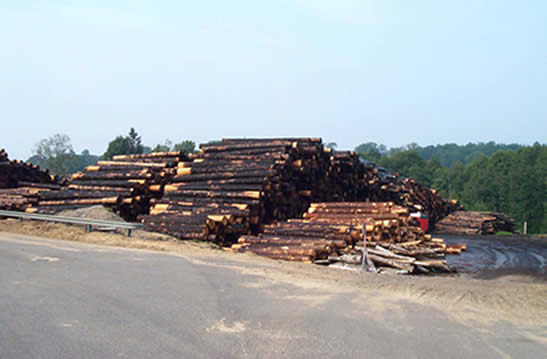
Log pile.
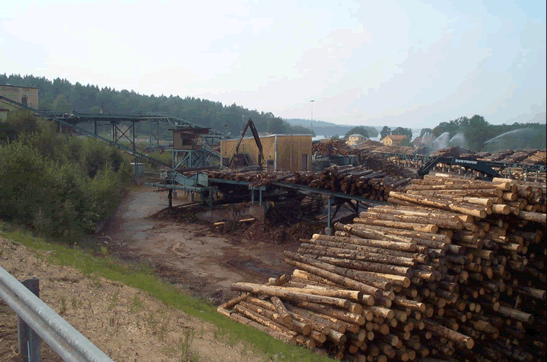
Log debarking.
Sawdust – a by-product of sawmilling.
Sawdust is moved with a large bucket loader from the sawmill to the pellet plant.
Sawdust is then moved to a large silo.
A large drum dryer reduces sawdust moisture content from 55% to 10%s
Dried sawdust is moved by conveyer to the pellet plant.
One of two Danish Sprout-Matador pellet mills, combined capacity seven tons per hour.
Sawdust enters at the top, pellets are dropped on conveyor at bottom
.
Pellet mill.
Large electric motors are required to drive the mills.
Pellet dies, have an average service life of 1,000 - 1,500 hours.
An automatic bagging system is adjacent to the pellet mills.
The easy-to-handle, 16-Kg pellet bag was designed for the Swedish market.
The bagged pellets are automatically loaded on pallets.
The pellet bag labels target multi-country markets.
Pallets of pellets outside warehouse await the heating season.